4 Must-Know Facts About Oil Seals: Types, Uses, and Maintenance Tips
Introduction
Oil seals, also known as rotary shaft seals or lip seals, are unsung heroes in industries like automotive, aerospace, manufacturing, and heavy machinery. These small but mighty components prevent fluid leaks, protect critical parts like bearings and shafts, and ensure machinery runs smoothly. Whether you’re maintaining a car engine or a hydraulic system, understanding oil seals can save you from costly repairs. Here are four essential facts about oil seals—covering their purpose, types, performance factors, and maintenance—to help you maximize their lifespan.
What Are Oil Seals and Why Are They Vital?
Oil seals are precision-engineered barriers that keep lubricants (like oil or grease) inside mechanical systems while blocking contaminants such as dust, dirt, and moisture. By protecting bearings, shafts, and gears, they ensure optimal performance and extend equipment life. Beyond leak prevention, oil seals maintain internal pressure, reducing wear and tear on moving parts.
Why Oil Seals Matter
Without reliable oil seals, machinery faces risks like corrosion, rust, and premature failure. For example, a 2022 industry report found that 60% of bearing failures stem from inadequate sealing, highlighting their critical role.
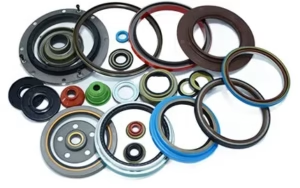

1. The Role and Purpose of Oil Seals
Oil seals serve three main functions:
- Leak Prevention: They stop lubricants from escaping, ensuring consistent lubrication.
- Contaminant Protection: They block dirt, water, and debris from entering sensitive components.
- Pressure Regulation: They maintain system stability under varying conditions.
These roles make oil seals indispensable for parts like crankshafts, gearboxes, and hydraulic pumps.
Table: Oil Seal Functions at a Glance
Function | Benefit |
---|---|
Leak Prevention | Maintains lubrication levels |
Contaminant Protection | Reduces wear on bearings and shafts |
Pressure Regulation | Enhances system efficiency |
2. Types of Oil Seals and Their Uses
Oil seals come in various designs and materials, each suited to specific conditions. Here are the most common types:
- Single-Lip Oil Seals: Ideal for low-contamination environments, like small motors.
- Double-Lip Oil Seals: Extra protection for high-pressure or dusty settings, common in automotive engines.
- Spring-Loaded Oil Seals: Built for dynamic applications with high speeds, such as industrial pumps.
Materials like rubber, silicone, PTFE (polytetrafluoroethylene), and Viton are chosen based on temperature, pressure, and chemical exposure. For instance, PTFE seals handle temperatures up to 260°C, making them perfect for aerospace.
Choosing the Right Oil Seal
Industry | Recommended Seal | Why? |
---|---|---|
Automotive | Double-Lip, Rubber | High pressure and heat resistance |
Aerospace | Spring-Loaded, PTFE | Extreme temperatures |
Heavy Machinery | Metal-Housed, Viton | Durability in tough conditions |
3. Factors Impacting Oil Seal Performance
Oil seal longevity depends on several factors:
- Temperature: Extreme heat (above 150°C for rubber seals) or cold can cause cracking or shrinkage.
- Pressure: High pressure (e.g., >500 PSI) may deform seals, leading to leaks.
- Speed: High rotational speeds increase friction, wearing seals faster.
Other culprits include improper installation (e.g., misalignment) and contamination during storage or use.
Preventing Contamination
Store seals in sealed, heavy-duty plastic bags or bins away from dust. Cleanliness during installation is key—debris can create tiny gaps, compromising the seal.
Common Failure Causes
- Misaligned installation (40% of failures, per industry surveys).
- Excessive heat or friction degrading materials.
- Contaminants breaching the seal.
4. Maintenance and Replacement Tips
Regular checks can catch oil seal issues early. Watch for:
- Leakage: Puddles or stains under machinery.
- Wear: Cracks, fraying, or hardening of the seal.
- Contamination: Dirt or moisture inside the sealed area.
Installation Best Practices
- Use a proper press tool to align seals evenly—uneven shearing signals a problem.
- Avoid over-lubricating, which can attract debris.
Rubber vs. Metal Housing Seals
- Metal Housing: Rigid and durable, ideal for steel casings in heavy-duty setups.
- Rubber Housing: Flexible and rust-resistant, perfect for thermal expansion or damaged housings.
Pro Tip: For high-vibration environments, opt for metal-housed seals to prevent loosening.
Conclusion
Oil seals—whether radial seals, lip seals, or hydraulic seals—are vital for leak prevention, equipment protection, and system efficiency. By understanding their types, performance factors, and maintenance needs, you can choose the right seal and keep your machinery running longer. Invest in high-quality seals from trusted suppliers, and schedule regular inspections to avoid downtime.
FAQ: Your Oil Seal Questions Answered
Q: How do I know if my oil seal is failing?
A: Look for oil leaks, unusual noises, or visible cracks in the seal.
A: Look for oil leaks, unusual noises, or visible cracks in the seal.
Q: What’s the best oil seal for high temperatures?
A: PTFE or ffkm seals excel in heat, tolerating up to 260-300°C or more.
A: PTFE or ffkm seals excel in heat, tolerating up to 260-300°C or more.
Q: How often should I replace oil seals?
A: It depends on usage—check every 6-12 months or per manufacturer guidelines.
A: It depends on usage—check every 6-12 months or per manufacturer guidelines.
Call to Action
Need help picking the perfect oil seal? Visit drorubber.com or reach out via WhatsApp: +0086 15815831911 or WeChat: +0086 13784044874 for expert advice!